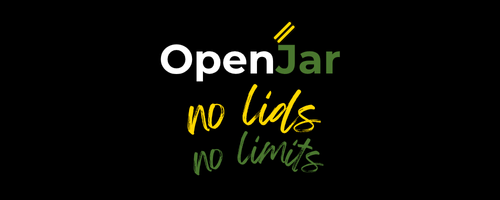
Why Your ERP Implementation Failed (and How to Fix It Midstream)
Switching ERPs is one of the most painful things your business can do. It's like doing open-heart surgery while running a marathon. So if you didn’t have a damn good reason to start in the first place, chances are the project was doomed before kickoff.
That said, even the best reasons and cleanest implementations hit roadblocks. If you're midstream, neck-deep in confusion, delays, and regret — you're not alone. But it can be fixed. Here's how.
1. Don’t Expect Perfection — Expect Change
Your old system had problems. That’s why you’re switching. But if you expect your new ERP to work exactly like the old one, you’ve missed the point.
Too many companies try to force the new system to behave like the one they just left. They customize, override, and bolt-on until they’re right back where they started — just with a bigger invoice and fancier UI.
Stop bending the system to your old ways. Use this chance to upgrade your processes to fit modern best practices. Your ERP already has guardrails for how smart companies operate — lean into that.
2. The EMS Workforce Doesn’t Love Change. Invest Accordingly.
Most EMS companies run on tribal knowledge. “That’s just how we’ve always done it” is the unofficial training manual. A new ERP kills that.
You can’t just install software and expect it to stick. You need serious training. Not one Zoom call. Not a PDF. We’re talking hands-on, repeated, role-specific coaching.
3. If You Didn’t Prioritize It, It’s Not Going to Work
ERP implementation is a full-time job. That job usually lands on your best people — the ones already drowning in daily operations. If they’re stretched thin, the implementation suffers.
No consultant can make your ERP successful without your team’s involvement. Clear calendars, shift workloads, and make this a company-wide priority.
4. Don’t Let Data Migration Derail the Whole Thing
If you're still struggling to define your part numbers or work centers halfway through the project, that's a red flag.
Worse, some teams treat ERP implementation as a chance to finally clean up their data. That’s a trap.
An ERP project is not a data cleanup project. Clean your data before or after. Not during.
5. Go-Live ≠ Perfection. It Means You Can Run the Business.
You don’t need every bell and whistle on Day One. The real Go-Live checklist:
- Can we take orders?
- Can we ship product?
- Can we invoice customers?
If yes, go live. And then keep working on figuring out the rest.
6. You Need Someone Who’s Done This Before
ERP systems are deep. EMS operations are messy. The overlap? Even messier.
If you don’t have someone who understands both ERP and EMS, you're making high-stakes decisions blindfolded.
Bring in a guide who knows both. They’ll help you avoid mistakes that haunt your business for years.
Bottom Line
ERP failure isn’t final. But fixing it means focusing on what matters:
- Stop clinging to the past.
- Prioritize your people.
- Stay ruthless about value.
- Get real help.
Don’t waste the pain. Use it to build something better.